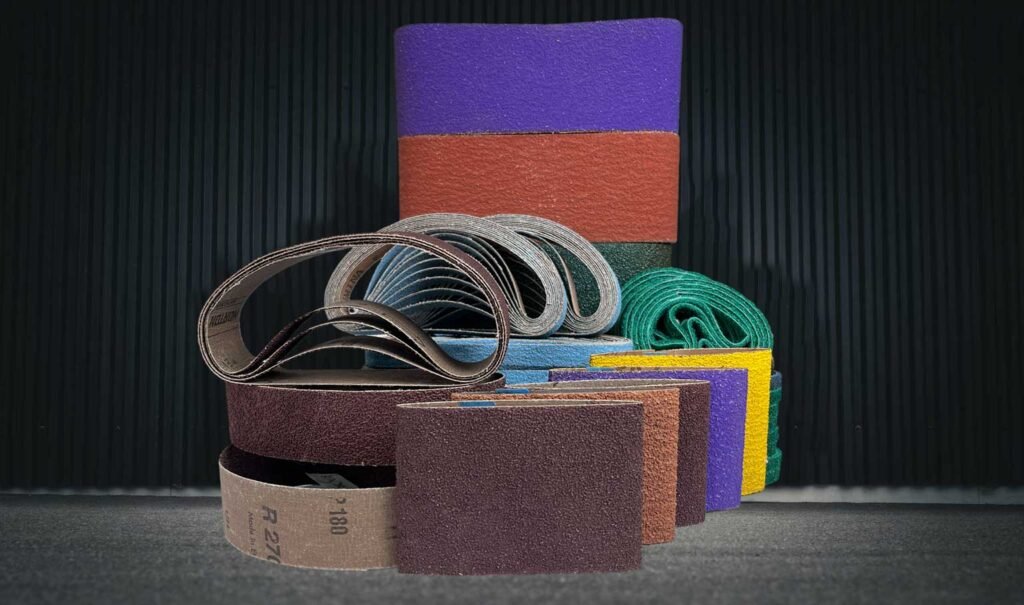
When it comes to sanding steel, choosing the right abrasive belt is crucial for achieving efficient and high-quality results. Whether you’re working in an industrial setting or a manufacturing plant, using the correct abrasive belt can significantly affect the durability of your equipment, the precision of your work, and your overall production efficiency. In this article, we’ll explore the best abrasive belts for steel grinding, with a focus on technical specifications, use cases, and buying tips to ensure your steel sanding tasks are completed effectively.
Introduction: The Importance of Choosing the Right Abrasive Belt
Steel is a commonly used material in various industries such as automotive manufacturing, metalworking, and construction. However, sanding steel requires specialized abrasive materials that can withstand high pressures, remove excess material efficiently, and provide a smooth finish. Using the wrong abrasive belt can lead to inefficient performance, increased wear on machinery, and lower product quality.
This guide will help you understand the different types of sanding belts available for steel, highlight their specific uses, and provide tips on choosing the best belt for your needs.
- Types of Abrasive Belts for Steel Sanding
When selecting an abrasive belt for steel sanding, it’s essential to consider the material’s characteristics, including hardness, the type of abrasive used, and the belt structure. Here are the most suitable belts for sanding steel:
1.1 Zirconia Abrasive Belts
Best for Heavy-Duty Steel Grinding
Zirconia abrasive belts are a top choice for heavy-duty grinding, especially when dealing with steel materials. These belts are known for their durability and aggressive cutting power, making them ideal for initial stock removal and coarse grinding.
Technical Parameters:
Abrasive Material: Zirconia Alumina
Grit Range: 24-60 grit for aggressive stock removal; 60-120 grit for finishing
Belt Structure: Heavy cloth backing, usually with an open coat for efficient cooling
Key Benefits:
Longer lifespan than aluminum oxide belts (up to 30% more durable, according to a 2022 3M Technical Report)
Excellent for grinding hard materials like steel, stainless steel, and even high-tensile alloys
Efficient heat dissipation, reducing the risk of overheating and damage to the workpiece
Recommended Use Cases:
Ideal for grinding steel pipes, beams, and other large steel components
Suitable for welding seam removal and deburring tasks
1.2 Ceramic Abrasive Belts
Best for Tough Steel Stock Removal
Ceramic abrasive belts excel at heavy-duty grinding tasks involving large amounts of material removal. These belts are particularly effective when working with tougher steels or when high stock removal is required without compromising finish quality.
Technical Parameters:
Abrasive Material: Ceramic grain
Grit Range: 36-80 grit for stock removal; 80-120 grit for finish grinding
Belt Structure: Closed coat with ceramic grain for longer-lasting sharpness
Key Benefits:
More aggressive than zirconia belts, making them ideal for tough stock removal
Maintains a sharp cutting edge for longer periods, improving efficiency and reducing the need for frequent belt changes
Superior in maintaining surface finish quality, especially for tougher materials like carbon steel
Recommended Use Cases:
Ideal for applications where large quantities of material must be removed, such as grinding steel billets or forgings
Perfect for high-pressure grinding tasks that require both power and precision
1.3 Aluminum Oxide Abrasive Belts
Best for Cost-Effective Steel Sanding
While zirconia and ceramic belts are designed for heavy-duty applications, aluminum oxide belts are a more economical option for general-purpose steel sanding tasks. These belts are perfect for less demanding tasks where cost-effectiveness is a priority.
Technical Parameters:
Abrasive Material: Aluminum oxide
Grit Range: 40-150 grit for light to medium stock removal; 150-400 for finishing
Belt Structure: Flexible cloth or paper backing, ideal for less aggressive sanding
Key Benefits:
Cost-effective and readily available
Good balance of cutting power and surface finish
Suitable for a wide range of applications from deburring to fine finishing
Recommended Use Cases:
Ideal for general-purpose sanding, cleaning, and surface preparation on steel
Suitable for use in workshops where speed and cost are more important than aggressive material removal
1.4 Stacked Abrasive Belts
Best for Automatic Grinding Machines
These belts offer high resistance to wear, making them ideal for applications where frequent belt changes can cause inefficiencies.
Technical Parameters:
Grit Range: 60-600 Grit
Belt Structure: Reinforced polyester backing with a closed coat
Key Benefits:
Excellent for automated grinding tasks
Resists stretching and wear, making them ideal for high-speed applications
Reduces maintenance downtime by extending belt life
Recommended Use Cases:
Ideal for continuous production lines where high-speed grinding is necessary, such as in the automotive or steel processing industry
- Choosing the Right Belt for Your Steel Sanding Needs
Choosing the correct abrasive belt for steel involves considering the specific requirements of your project. Below are some key factors to consider when making your selection:
https://sandingbeltdepot.com/product-category/abrasive_belts/ceramic_sanding_belts2.1 Consider the Material Hardness
Steel comes in many grades, and its hardness will impact the type of belt you should choose. Harder grades of steel, such as stainless steel or tool steel, benefit from more aggressive abrasives like zirconia or ceramic belts. Softer steel grades may be adequately handled by aluminum oxide belts.
2.2 Grit Size for Optimal Results
The grit size of the abrasive belt plays a significant role in determining the finish and material removal rate. For initial stock removal, coarser grits (24-60) are ideal, while finer grits (80-220) are better suited for finishing and polishing tasks.
2.3 Production Speed
If you’re working with automated machinery, polyester-backed belts may be the best choice as they can withstand continuous high-speed sanding without significant wear.
- Sanding Tips for Steel
To maximize the performance of your sanding belts, here are some essential tips:
Monitor Belt Speed: High-speed grinding generates more heat, so ensure your machine operates at the correct belt speed for the material and type of abrasive.
Cooling: Overheating can damage both the steel and the abrasive belt. Use water or coolant when appropriate to reduce heat buildup.
Pressure: Apply moderate pressure during sanding to prevent excessive wear on the belt and to achieve a consistent finish.
- FAQ: Common Questions about Sanding Steel
Q1: Can I use the same abrasive belt for all types of steel?
A1: No, different types of steel require different abrasives. Harder steels need more aggressive abrasives like ceramic or zirconia, while softer steels can be sanded with aluminum oxide belts.
Q2: How do I know when it’s time to replace my sanding belt?
A2: If you notice a decrease in cutting performance or the belt is excessively worn down, it’s time to replace it. Regular inspection will help prevent inefficient sanding.
Q3: Can I use the same belt for both rough grinding and finishing?
A3: It’s best to use different belts for rough grinding and finishing. Rough grinding requires a coarser grit, while finishing requires finer grits for a smooth surface.
Conclusion
Choosing the right abrasive belt for sanding steel is essential for achieving high-quality results, whether you’re working in an industrial setting or with automated machinery. Zirconia, ceramic, aluminum oxide, and Stacked abrasive belts each serve a specific purpose depending on your grinding requirements. By understanding the characteristics of each type of belt, you can make an informed decision that maximizes your productivity and enhances the final surface finish of your steel parts.
For optimal performance, always consider the material hardness, grit size, and production environment when selecting your abrasive belts.
(This article is based on AI generation and is for reference only. For specific usage effects, please communicate with us to purchase samples and then compare with the actual test results.)